
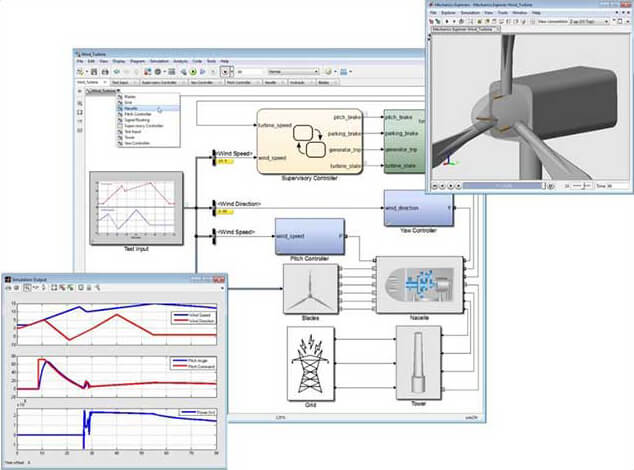
However, rather than stop heating when target is reached, “I” attempts to drive the cumulative error to zero, resulting in an overshoot. For example, if the oven remained below temperature, “I” would act to increase the head delivered.
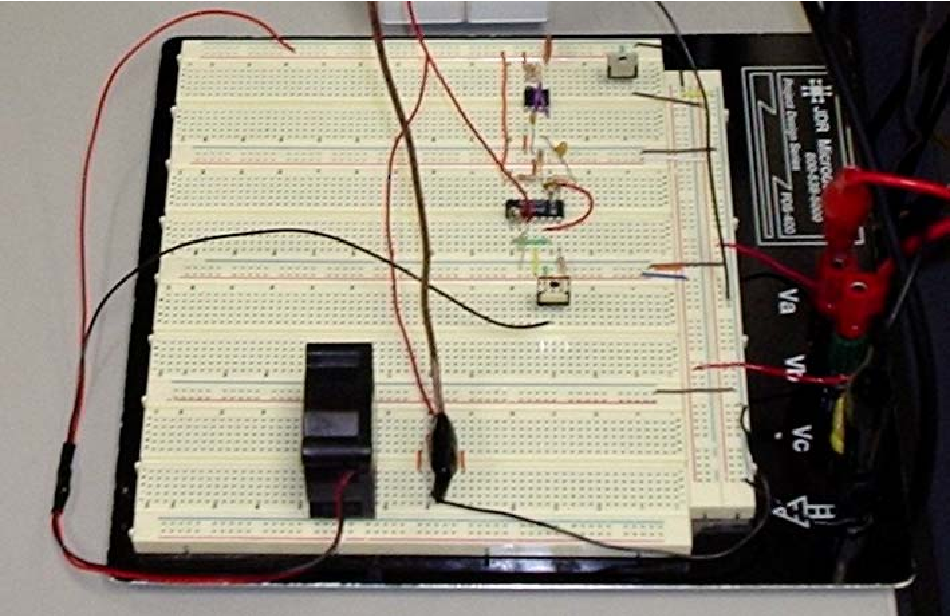
Based on the difference between these values a correction factor is calculated and applied to the input. The working principle behind a PID controller is that the proportional (“P”), integral (“I”), and derivative (“D) terms must be individually adjusted or ‘tuned’. The basics of a closed loop system involve a sensor to measure the output, a control unit to compare the output to the desired output, and an actuator to modify the system’s behavior or operation. This type of system is useful for controlling systems with many variables and ensuring accurate and consistent performance. In a closed loop system, the output is compared to the desired output and any differences are used to modify the system’s behavior or operation. It is also known as a feedback control system. It is recommended in systems where the load changes often and the controller is expected to compensate automatically due to frequent changes in setpoint, the amount of energy available, or the mass to be controlled.Ī closed loop system is a type of automatic control system in which the output of the system is used to modify the behavior or operation of the system. PID controllers are best used in systems which have a relatively small mass and those which react quickly to changes in the energy added to the process. The purpose of a PID controller is to force feedback to match a setpoint, such as a thermostat, that forces the heating and cooling unit to turn on or off based on a set temperature. PID control keeps the actual output from a process as close to the target or setpoint output as possible. It’s practically ubiquitous as a means of controlling temperature and finds application in a myriad of chemical and scientific processes as well as automation. PID control is a well-established way of driving a system towards a target position or control parameters.

PID controllers use a control loop feedback mechanism to control process variables and are the most accurate and stable controller. A PID (Proportional – Integral – Derivative) controller is an instrument used by control engineers to regulate temperature, flow, pressure, speed, and other process variables in industrial control systems.
